Время пребывания предмета труда в процессе производства с момента его поступления в обработку до выхода в виде готовой продукции составляет производственный цикл. Так как производственный процесс изготовления изделия состоит обычно из нескольких стадий, или фаз, например производственный цикл сушки, производственный цикл сборки изделий и т.д.
Каждому производственному циклу свойственна определённая продолжительность и структура. Под продолжительностью производственного цикла понимают время, в течение которого предмет труда подвергается обработке с момента запуска его в производство до момента выхода готового продукта; под структурой понимают состав цикла по видам операций и соотношение затрат времени на их выполнение, включая все перерывы.
Продолжительность производственного цикла определяется в календарных единицах времени – в месяцах, днях, часах или минутах - и состоит из рабочего периода и времени перерывов в производстве. Рабочий период складывается из времени выполнения технологических операций tос, времени выполнения вспомогательных операций tвс и времени камерной сушки tc. Время перерывов в производстве складывается из технологических и организационных перерывов. К технологическим относятся перерывы tт которые связаны с процессами, не требующими применения труда (выдержка деталей после сушки, склеивания, отделки, облицовывания). К организационным относятся: перерывы tв обусловленные режимом рабочего времени (нерабочие смены и дни, обеденные и другие регламентированные перерывы); межоперационные перерывы tмеж, когда предмет труда пролеживает у рабочих мест; прочие перерывы по организационным причинам tорг , например, из-за недостатка инструмента, электроэнергии. Таким образом, продолжительность производственного цикла в общем виде может быть выражена следующей формулой:
T = tос + tвс + tс + tт + tв + tмеж + tорг (2.1)
Организационные перерывы при плановом расчете продолжительности цикла не учитываются.
Можно отдельно рассматривать продолжительность производственного цикла одной детали, партии деталей, изделия.
Продолжительность производственного цикла одной детали всегда соответствует сумме продолжительности всех технологических операций, вспомогательных операций и перерывов, потому что отдельная деталь, пройти все стадии операции только последовательно.
Продолжительность производственного цикла партии деталей соответствует времени, которое затрачивается на все операции технологического процесса (технологический цикл) с последующим прибавлением времени на вспомогательные операции и перерывы.
Операционный технологический цикл партии деталей (дни)
(2.2)
nд - число деталей в партии;
tобр - время по нормам на обработку одной детали, мин;
Kн - коэффициент выполнения норм на данной операции;
nр - число рабочих мест, на которых параллельно выполняется данная операция;
Tсм - календарный фонд времени одной смены, мин;
S - сменность (число смен).
Для уменьшения продолжительности операционного технологического цикла необходимо сокращать время на обработку одной детали и расширять фронт работ, т. е. увеличивать число станков и рабочих мест, одновременно занятых обработкой партии деталей.
Продолжительность технологического цикла партии деталей по всем операциям технологического процесса зависит от вида движения обрабатываемых предметов труда, который может быть последовательным, параллельным и параллельно-последовательным (смешанным).
При последовательном движении партии деталей в технологическом процессе каждая последующая операция начинается с того, как выполнена предыдущая операция над всеми деталями данной партии. При этом с операции на операцию все детали партии передаются одновременно, после окончания их обработки.
Продолжительность технологического цикла при последовательном движении может быть определена по формуле
Tц = nд ∑ tд (2.3)
Где ∑ tд – сумма продолжительностей всех операций, которые проходит обрабатываемая деталь, с учётом выполнения норм и числа параллельно занятых рабочих мест по каждой операции.
Последовательное движение партии деталей в технологическом процессе является наименее эффективным, потому что получается самый длинный технологический цикл. В результате увеличиваются средства, находящиеся в незавершенном производстве, и замедляется их оборачиваемость.
При параллельном движении партии деталей в технологическом процессе каждая деталь после выполнения одной операции сразу, без перерыва во времени, передается на другую, не ожидая окончания обработки всей партии. В этом случае все детали данной партии находятся одновременно в обработке на различных местах в последовательности технологического процесса. Определяющее воздействие на продолжительность технологического цикла оказывает время, потребное для выполнения наиболее трудоемкой, длительной операции tгл.
Продолжительность технологического цикла при параллельном движении может быть определена по формуле
Tц = ∑ tд + (nд - 1) tгл (2.4)
Параллельное движение партии деталей в технологическом процессе является наиболее эффективным, потому что получается самый короткий технологический цикл, наименьший объем незавершенного производства и наиболее быстрая оборачиваемость средств. Однако применение параллельного движения возможно лишь в тех случаях, когда разница во времени между смежными операциями не велика и не вызывает больших простоев из-за ожидания деталей.
При параллельно-последовательном движении партии деталей в технологическом процессе обработка партии на каждой последующей операции начинается раньше, чем заканчивается обработка всей партии на предыдущей операции. В зависимости от соотношения времени выполнения операций последовательная операция может начинаться сразу, как только первая деталь пройдёт предыдущую операцию, или после некоторого накапливания обработанных деталей для последующей операции, чтобы избежать перерывов в работе.
Таким образом, при параллельно-последовательном движении партию деталей с операции на операцию передают частями; обрабатываемая часть партии одновременно проходит несколько операций, и начало каждой операции рассчитано так, чтобы обеспечить непрерывность обработки партии.
Продолжительность технологического цикла при параллельно-последовательном движении может быть определена по формуле
Tц = ∑ tд + (nд - 1) (∑tб - ∑tм) (2.5)
Где ∑tб и ∑tм – сумма всех больших и меньших операций
Большая операция и меньшая определяется при сравнении данной продолжительности с предыдущей и с последующей
или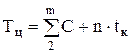
tк – время выполнения последней операции процесса.
Время смещения определяется следующим образом:
если tm-1>tm, то Cm=n×tm-1-(n-1)×tm; (2.7)
если tm-1<tm, то Cm=tm-1.
Упрощённые графики технологического цикла по трём формам движения деталей от операции к операции представлены на рис2.1.
а)

в)
Рис. 2.1. Упрощенные графики технологического цикла по трём формам движения деталей от операции к операции: а) последовательная форма движения; б) параллельная форма движения; в)смешанная форма движения.
Пд – количество деталей в партии; р – размер передаточной партии с операции на операцию.
Сложные производственные процессы имеют место при изготовлении изделий. Помимо циклов производства отдельных деталей и заготовок в длительность цикла изготовления изделия (комплекса) входят циклы сборки отдельных сборочных единиц, изделия в целом, а также продолжительность отделочных операций, обкатки, испытаний и т.п.Производственный цикл сложного процесса выражает общую продолжительность комплекса скоординированных во времени простых процессов, входящих в сложный процесс.
Длительность цикла сложного процесса устанавливается на основании циклового графика, который строится по схеме сборки изделия (веерной диаграмме). Отправным моментом построения служит дата выпуска готового изделия (дата завершения сборки аппарата). Цикловой график, таким образом, строят в направлении, обратном ходу производственного процесса. В результате рассчитывается коэффициент параллельности, равный:
, (2.8)
Тцизд – длительность цикла по цикловому графику.
Также длительность цикла сложного процесса можно определить при помощи сетевого графика.
Методы сетевого планирования и управления позволяют оптимизировать производственный процесс как во времени, так и по стоимости. Эти методы основаны на построении сетевой модели определённого комплекса работ.
Сетевая модель – это графическое изображение технологической последовательности и связи событий, каждое из которых выражает результат и момент окончания входящей в него одной или нескольких работ. Пример сетевой модели представлен на рис. 2.2.
Работа – это процесс, действие, приводящее к получению определённого результата, т.е. свершению события.
Различают работу действительную, т.е. требующую затрат труда и ресурсов и фиктивную, представляющую логическую связь между двумя событиями.
![]() |
Рис. 2.2 - Пример сетевой модели
Действительная работа обозначается сплошной стрелкой, фиктивная – пунктирной стрелкой, событие – кружком.При построении сетевых моделей (графиков) необходимо соблюдать следующие условия:
график не должен иметь замкнутых контуров;
график не должен иметь тупиков, т.е. событий (кроме завершающего), из которых не выходит ни одна работа;
график не должен иметь более одного исходного события.
Сетевая модель, в которой даны необходимые количественные характеристики работ и событий, называется сетевым графиком.
Для расчёта сетевых графиков применяется ряд показателей (параметров): путь, критический путь, продолжительность работы, раннее начало ж раннее окончание работы, позднее начало и позднее окончание работы, резервы времени.
Определения этих параметров и их расчёт даются на лекционных занятиях и здесь не повторяются.
Порядок расчёта основных параметров.
а) Ранний и поздний сроки свершения начального события принимают равными нулю (Трi=Тni = 0).
б) Оcущеcтвляют «движение» от исходного (0) события к завершающему и последовательно определяют ранние сроки свершения конечных событий
Трj = max (Трi + tij), (2.9) где tij – продолжительность работы от i – начального события до j – конечного.в) Поздний срок завершающего события принимают равным полученному значению его раннего срока свершения Тnj=Трj.
г) Осуществляют «движение» от завершающего события к исходному и определяют поздние сроки свершения начальных событий
Тni = min (Тnj - tij), (2.10)
д) Выявляют критический путь.
е) Определяют резервы времени событий R, работ Rij и пути Rl.
Резерв времени события R=Тn-Тр, (2.11)
Для событий, лежащих на критическом пути R=0. Полный резерв времени Rnij= Тnj- Трi - tij (2.12)Свободный резерв времени Rcij= Тpj- Трi - tij (2.13)
Резерв времени пути Rl =tkp-tl, (2.14)
где tkp, tl – длина (продолжительность) критического и анализируемого пути.
Результаты расчётов заносят в таблицу.Сетевую модель можно рассчитать графически. Тогда каждое событие (кружок) разделяется на четыре сектора (см. рисунок 2.3), в каждом из которых пишется соответствующее значение, а над работой указывается её продолжительность tij.
![]() |
I – порядковой номер события.
II – ранний срок.
III – поздний срок.
IV – резерв времени свершения события. Рис.2.3 После расчёта основных параметров сетевого графика полученную модель можно оптимизировать с учётом трудоёмкости выполнения работ на критическом пути и других путях. Межоперационные перерывы (пролеживание) характерны для последовательного и параллельно-последовательного движений. При последовательном движений время на межоперационные перерывы перекрывается основным технологическим временем. Продолжительность межоперационных перерывов при параллельно-последовательном движении: (2.15)
Продолжительность перерывов tв, связанных с режимом рабочего времени, учитывается путем увеличения продолжительности технологического цикла на число часов или смен, в течении которых партия деталей не обрабатывается, либо путем ия этой продолжительности на коэффициент режима рабочего времени К'реж, характеризующий указанные перерывы. Коэффициент режима зависит от сменности и определяется по формуле:
(2.16)
|
Тц = Тзаг + Тсуш + Тмаш + Тсбор + Тотд (2.17)
Наиболее трудоемкой деталью обычно считают ту, которая требует больше времени на обработку в машинно-облицовочном цехе.
Продолжительность и структура производственного цикла имеют большое значение в экономике предприятия. От продолжительности производственного цикла зависят сроки выполнения заказов, размер незавершенного производства и оборотных средств, потребность в производственных площадях и степень использования основных средств, что в свою очередь влияет на основные показатели качества работы предприятия — производительность труда и себестоимость продукции.
Сокращение продолжительности производственного цикла является одной из основных задач организации и планирования производства. Для сокращения продолжительности производственного цикла необходимо: снижение затрат труда по всем стадиям производства; увеличение фронта работ и переход на более эффективный порядок организации технологического процесса; снижение времени на перерывы и улучшение режима работы предприятия; улучшение организации производства предприятия. Указанные мероприятия должны быть основаны на внедрении новой техники и передовой технологии, новых видов материалов, специализации предприятий.
Поможем написать любую работу на аналогичную тему